Flux core welding evolved from the MIG process but in this case, you have a wire filled with flux. The welding process produces an electric arc as the metal pieces are exposed to the wire electrode. As the flux wire melts during welding it holds the pieces together while protecting them from atmospheric oxidation.
The flux core welding process can be categorized into –one with shielding gas and another without. If you are working outdoors then it makes more sense to use the self-shielded flux core welding process while indoors use the one with shielding gas. The fluxing agents differ but their primary function is to protect the weld from oxidation and contamination from outside agents.
The flux core wire is at the center of this welding process. It is an electrode that contains a mixture of various fluxing agents, deoxidizers, Ferro-alloys and metal powders. During welding, you can either use carbon dioxide as a shield or rely on the flux for shielding. If you are to compare the welds between these two techniques, using carbon dioxide offers a more penetrative arc.
Before we check out how to reduce flux core welding spatter, we may want to learn something on the root cause for spatter.
Common causes for spatter and solutions
Spatter is a common feature in MIG welding. Sparks and spatter flying all over the weld characterize it. If you do not have the right amount of clothing, spatter can cause burns to your skin and probably find its way to your eyes. Spatter also leads to lots of welding clean up and you waste materials. Understanding what causes it is the first step in controlling it.
Improper settings
Everything has to be right when you are doing flux core welding. One of the first causes for spatter is incorrect amperage settings. The wire feed speed determines the kind of amperage you will be using. If you set too high then you will experience spatter. You can solve this in two main ways – lowering amperage (or wire reducing wire speed) or increasing voltage. You will need to constantly test the welds until you find the right settings.
Wire feeding problems
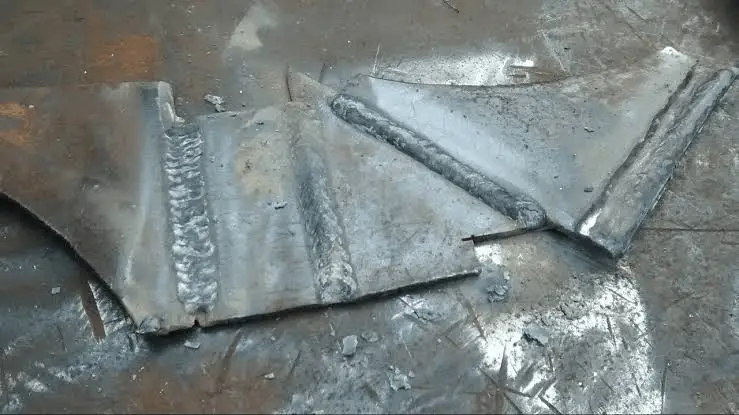
Wire feeding problems can either two forms – birdnesting or burnback. During burnback you have a too slow wire feed speed that causes the wire to melt at its contact tip hence forming a ball. It can also occur when you hold the welding gun too close to the metal pieces. It is recommended that you keep the contact tip distance to no more than 1 ¼ inches. In birdnesting, the wire becomes tangled hence preventing it’s been feeding. To mitigate this use U-groove or knurled V drive rolls in the wire feeder. The problem with the flux core welding wire is that it is softer hence easily compressed due to incorrect drive roll.
Contaminated surfaces
Before you can start welding it is prudent that you check the conditions of your work piece for any signs of dirt or rust. Contaminated pieces are a major cause for spatter. Also, ensure your work piece is free from any paint, grease or oil.
Too steep of work angle
The rule is the steeper the angles the more spatter you experience. How to hold the MIG gun is still up to debate among welders. Some go for dragging or pushing the gun, however, the correct position is that your push/drag angle should never exceed 15 degrees. Improper holding of the MIG gun will lead to the shielding gas been used unevenly on the weld. Work out on how to hold the gun properly if you are to decrease your rate of spatter.
Poor quality consumables
Low quality consumable wires can lead to MIG gun clogging as its diameter varies with what is recommended. This leads to the wire been fed to the gun at varying speeds hence the welder experiences less than perfect contact tip. When selecting the right consumable wire, do not always go for the most expensive. The wire should be high quality and suitable for your particular job.
Low quality shielding gas
This is not unusual but it does happen that you will purchase some bad shielding gas that will increase your rate of spatter. MIG gas is often a mixture of other gases so you will find the gas labeling showing the various percentages. The right mixture is not that straightforward. Higher carbon dioxide content leads to higher penetration rates but at the expense of getting more spatter. Having more argon is good as it leads to a smoother arc. Ensure you are getting the right mixtures.
Equipment issues that you can adjust to reduce spatter
Work clamp
After you have set the above the next step would be to check out your working areas. If you have a weak connection in the work clamp it will cause fluctuations in the welding arc. To solve this, begin by checking the connecting cables for any looseness, then ensure the work clamp is properly positioned into the worktable. The work clamp should be positioned as close to the weld as possible for the best results. Alternatively, you may be required to get a higher quality clamp if you want better welding results.
Wire feed issues
Here you need to check out your drive roller and the wire feed tension. Lose wire feed tension often leads to drive roller slippages. You may also want to clean off any dust that could have accumulated on the drive rollers and onto the wire guide. A proper roller is the one when the tensioners are disengaged allows one to move the wire back and forth. You can use compressed air to any liner that is flowing towards the gun end.
Shielding gas problems
The shielding gas is primarily there to protect your arc from any outside contaminants while at the same time stabilizing it. However, loose connections can prevent the gas from reaching the gun hence you may experience more spatter and unstable arc. To check that the gas is properly flowing, first disengage the wire feed tensioner then check the gun nozzle for sounds. If nothing is happening, you may want to check the entire gas connections from the gas valves to the welder connections. If there is any spatter that has found its way to the gun nozzle then you may experience gas flow restrictions.
Worn out contact tips
This is very uncommon as the tips are meant to last a lifetime. But, with continued usage you may notice some saw like impressions on the contact tips. If this happens replace it with either a .030˚ tip or .035˚ tip.
Benefits of using flux core welding
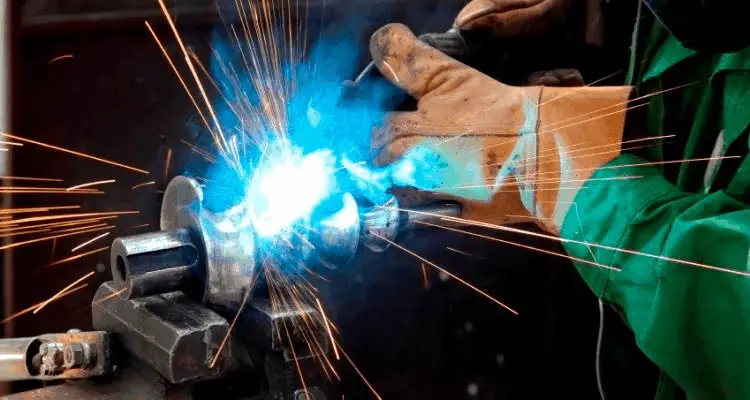
One of the reasons to use flux core welding as opposed to MIG welding is that you do not a separate shielding gas. This means the flux core is the one that offers the gas when it is heated. It also has higher deposition rates when compared to the MIG welding. In the flux core, the electrodes are the alloying agents as such they are ideal for outside welding. You can use flux core shielding for most mild steel construction. Since you do not need carbon dioxide for shielding the welds produced by flux core welding are stronger than those for MIG welding.
The flux core welding process have more tolerance for dirt and scale and this makes them ideal for rusty metals. You also experience less weld spatter than the MIG but the weld appearance is less cleaner.
When it comes to industrial use, most fabricators will prefer the flux core welding due to its higher penetration rates. It also allows them to work with thicker joints. With a flux welding machine you can hold the torch in all manner of directions and this gives it more versatility than other welding techniques.
The problem with flux core welding is you need a greater skill level than the MIG. Firstly, you will need to know how to properly hold the welding torch. The deposit rate for the flux core welding is higher than that of MIG. In the MIG welding you get 8 pounds per wire per hour while for flux it is 25 pounds. If you have numerous projects that have deadlines then go with the flux core welding technique.
If you are trying out welding with a rusty or oily metal then you will enjoy using the flux core welding. For one, it does not necessarily need a clean joint for it to be used. This is unlike the MIG where you have to properly grind the surface before welding. Flux core will cut through mill scale, rust and other metal imperfections.
Conclusion
Spatter is irritating when you are welding joints. However, most of the flux core spatter is as a result of amperage settings. You will need to check out an amperage chart to know which amperage setting you will use for a particular metal. Contaminants like dirt and oil will influence your welding. It is proper to clean out the metallic surfaces before welding. For rust you can use grinding to loosen it.